Automation in medical device manufacturing: 5 reasons for automated medical device assembly
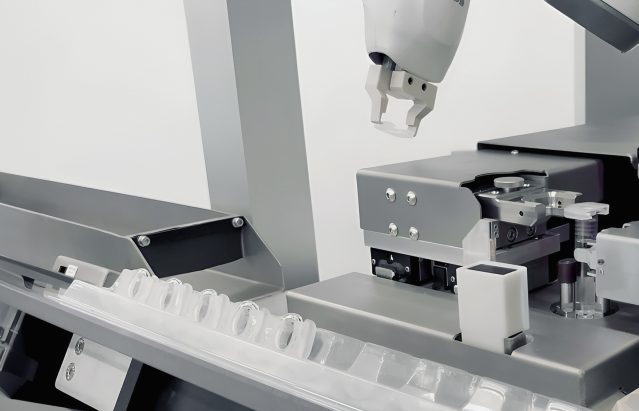
The assembly of medical devices is often much more complex than the manufacturing of traditional consumer goods. The reasons are manifold: from the large variety of different medical devices to the overall elevated standards in the life sciences and healthcare industry in terms of safety and compliance.
To ease the challenges in medical device manufacturing, many manufacturers are adopting automated robotic solutions for medical device manufacturing. But although there are possibilities to automate entire production processes, some manufacturers still count on manual labor.
In this article, we dissect the pragmatic reasons steering the medical device industry towards automation powered by robots. From precision in engineering to scalability, we will discuss the key factors shaping the future of automated medical device assembly.
1. Maximized precision and repeatability with automated medical device assembly
Automated medical device assembly brings forth a notable enhancement in precision and repeatability. Automated systems execute tasks with – literally – robotic accuracy, ensuring each device meets precise standards (e.g. prefilled syringes, PENs, auto-injectors, catheters, and other examples of medical devices).
The possibility to consistently replicate assembly processes eradicates variations, contributing to heightened product reliability. This combination of precision and repeatability not only satisfies the rigorous requirements of the medical industry but also allows improved manufacturing quality, profitability, and dependability.
Additionally, scalable assembly systems like the ESSERT MicroFactory can shorten time-to-market times, from prototyping to commercialization: Each module carries out one specific procedure, and with pre-series validation, steps can be integrated more conveniently.
2. Reduced staff requirements due to high autonomy
The integration of high-autonomy robotic systems in medical device assembly significantly diminishes the dependency on specially trained staff, which are often relied on in low-volume environments, or where standard equipment and systems might not be agile or careful enough.
Advanced automation solutions, on the other hand, are designed to operate with minimal human intervention, which is crucial in times when specialized staff is becoming increasingly hard to find. With intuitive programming and self-executing changeovers as well as re-calibration of advanced sensor technology, these systems empower a broader workforce, reducing reliance on niche expertise.
Additionally, automation can also lead to an increased safety level in manufacturing processes, as staff no longer have to carry out repetitive tasks in potentially dangerous environments.
Speaking of production environments: Cleanroom standards are another crucial aspect in medical device assembly. By relying on cleanroom-suitable, GMP-compliant robotic solutions, the risk of human error due to contamination can be reduced as well.
3. Enhanced compliance and full transparency in automated assembly
Robotic solutions in medical device assembly not only elevate process safety but also support manufacturers in ensuring compliance and full transparency. Automation facilitates adherence to stringent quality standards, e.g. issued by the FDA, by executing production processes consistently and reproducibly.
Moreover, manufacturing automation offers comprehensive data tracking, creating a transparent trail of each step in medical device manufacturing with increased traceability. Thus, medical device automation facilitates adherence to regulatory requirements in the medical manufacturing industry and supports pharmaceutical companies as well as contract manufacturing facilities to proactively address any issues.
4. Increased manufacturing productivity
Automation has great potential in enhancing assembly productivity – both in mass production and HMLV environments.
In mass production (low mix / high volume production), robotic solutions can streamline repetitive tasks, accelerate production cycles, and minimize downtime, which leads to an increased throughput.
But also in HMLV production settings, advancements in automation enable swift changeovers between product variants and components, reduce setup times, and optimize resource utilization, resulting in efficient cycle times for diverse product portfolios.
By automating key processes, manufacturers can unlock significant gains in productivity, irrespective of the production environment. However, there are certain aspects that need to be taken into account when looking for automated solutions in HMLV environments: First and foremost, they need to be more flexible.
5. Full flexibility and scalability of customizable robotic solutions
Embracing modular robotic solutions brings several advantages to medical device assembly automation, providing unparalleled flexibility and scalability. While not all automated robotic solutions are inherently modular, opting for flexible systems presents numerous benefits.
Solutions like the ESSERT MicroFactory enable seamless transitions between diverse production lines and scales, fostering adaptability and efficiency. Changeovers can be induced via software input and usually take less than 15 minutes. As each module carries out one specific step, it becomes easy to reconfigure or rearrange them, making it possible to produce various products in one production line.
The customizable design of automated assembly systems allows for high-speed adaptation to changing production needs, optimizing resource utilization. By prioritizing modular robotics, manufacturers gain a competitive edge, creating a cost-effective production environment capable of efficiently responding to industry trends and accommodating diverse product assembly requirements.
Automated processes in medical device manufacturing
Beyond assembly, automation proves instrumental in various facets of high-quality medical device manufacturing, from material handling to palletizing and labelling. Quality control benefits from precise inspections and defect detection, ensuring stringent standards. Automated testing expedites evaluations, checking device functionality and compliance.
In packaging, robotic systems handle intricate placement and labeling, preserving sterility and preventing damage during transit. Thus, automated processes in medical device manufacturing not only enhance operational efficiency, but also elevate product quality.
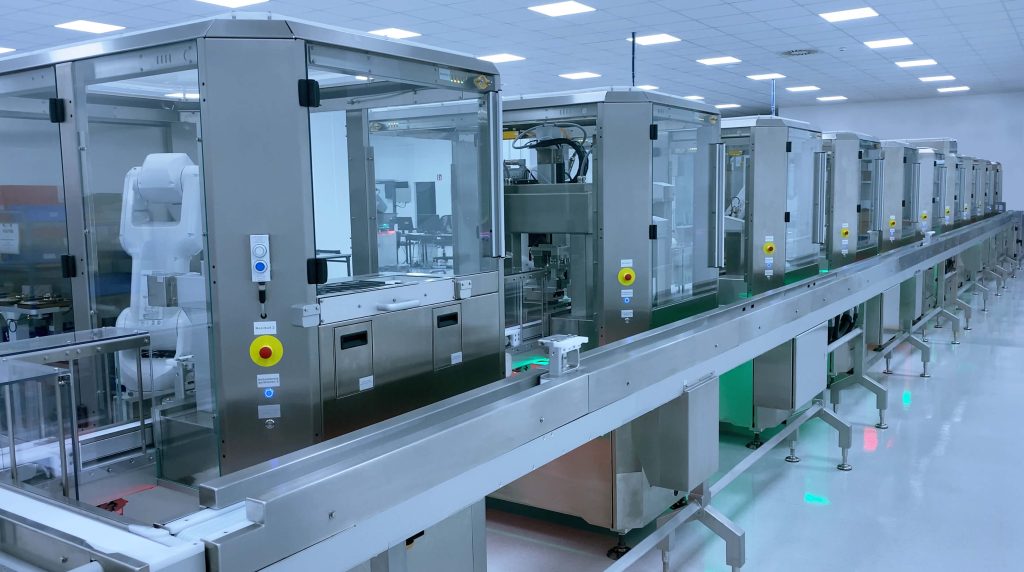
ESSERT MicroFactory – the automated medical device assembly platform
At the forefront of cutting-edge automated medical device assembly lines stands the ESSERT MicroFactory, an innovative assembly solution that redefines manufacturing standards. Uniting the capabilities of multiple ADVANCED Robotic Workstation modules, this system boasts exceptional adaptability and scalability. Nevertheless, ESSERT is a leading European robotic integrator, able to implement robotic solutions, assembly equipment, and tools by a variety of manufacturers on its standardized hardware and software platform.
Tailored for high mix / low volume (HMLV) production, the MicroFactory seamlessly navigates through diverse batch sizes and product types. Its modular design ensures a smooth transition between processes, accommodating changes effortlessly – e.g. when switching from prefilled syringe to PEN manufacturing. Governed by the Process Control Center, it ensures comprehensive control, visibility, and compliance with regulatory requirements.
With assets like autonomous commissioning, plug-and-produce functionality, and integration of manual workstations, the MicroFactory presents a holistic solution to automate medical device assembly with ease.