Medical device assembly – 7 crucial considerations for seamless production
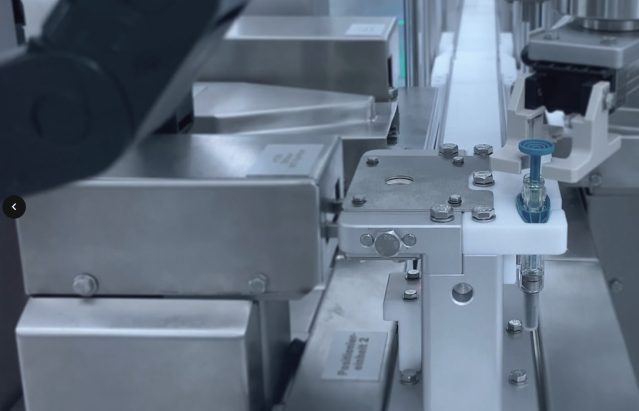
Medical device assembly is one of the areas that can profit substantially from automation. With challenges like GMP-compliance and changing customer demands that medical device manufacturing companies have to face, automated solutions have the potential to improve assembly lines and product quality.
In the following, we will focus on seven crucial consideration that have to be made to achieve a seamless production. Also, we will show how automation has not only the potential to improve mass production, but high mix / low volume productions in particular.
1. HMLV or LMHV?
There are two approaches in medical device manufacturing: high mix / low volume (HMLV) and low mix / high volume production (LMHV). While LMHV refers to a manufacturing process where large quantities of identical goods are produced, the term HMLV focuses on the production of a small number of customized goods.1
HMLV production typically operates on a smaller scale and requires the option for adjustability due to changes in customer demands. In contrast to LMHV productions in the healthcare industry, HMLV productions are less costly in terms of initial setup costs, but higher in per-unit cost. Machines for mass production tend to be bigger and expensive, but pay out more quickly over time due to the higher quantity of pieces that enter the market.2
2. Cleanroom conditions
The International Organization for Standardization (ISO) defines a cleanroom as a room, where the concentration of particles is controlled and their introduction to that room minimized by controlling airflow and other parameters.3
Cleanroom environments are crucial in the production of sterile pharmaceuticals and medical devices that pose a high patient risk, like catheters, stents, and cardiac by-pass systems.4
There are different cleanroom classes depending on the concentration of particles per m³ as defined by the ISO. Further, there are GMP equivalents which are not numbered but reach from grade A to D. The table below shows the different ISO classes and GMP grades, as well as the maximum particles per m³. As not only the number of particles is important in a cleanroom scenario, particle size is taken into account as well.
Cleanroom Standards5
ISO 13485 Class | Maximum particles/m3 | GMP grades | |||||
---|---|---|---|---|---|---|---|
>=0.1 µm | >=0.2 µm | >=0.3 µm | >=0.5 µm | >=1 µm | >=5 µm | ||
ISO 1 | 10 | 2 | |||||
ISO 2 | 100 | 24 | 10 | 4 | |||
ISO 3 | 1,000 | 237 | 102 | 35 | 8 | ||
ISO 4 | 10,000 | 2,370 | 1,020 | 352 | 83 | ||
ISO 5 | 100,000 | 23,700 | 10,200 | 3,520 | 832 | 29 | Grade A: zone for high-risk operations at rest and in operation Grade B: zone for aseptic preparation, filling and compounding at rest |
ISO 6 | 1,000,000 | 237,000 | 102,000 | 35,200 | 8,320 | 293 | |
ISO 7 | 352,000 | 83,200 | 2,930 | Grade B: zone for aseptic preparation, filling and compounding in operation | |||
ISO 8 | 3,520,000 | 832,000 | 29,300 | Grade C and D: clean area for less critical stages of manufacturing in rest and operation | |||
ISO 9 | 35,200,000 | 8,320,000 | 293,000 | Room Air |
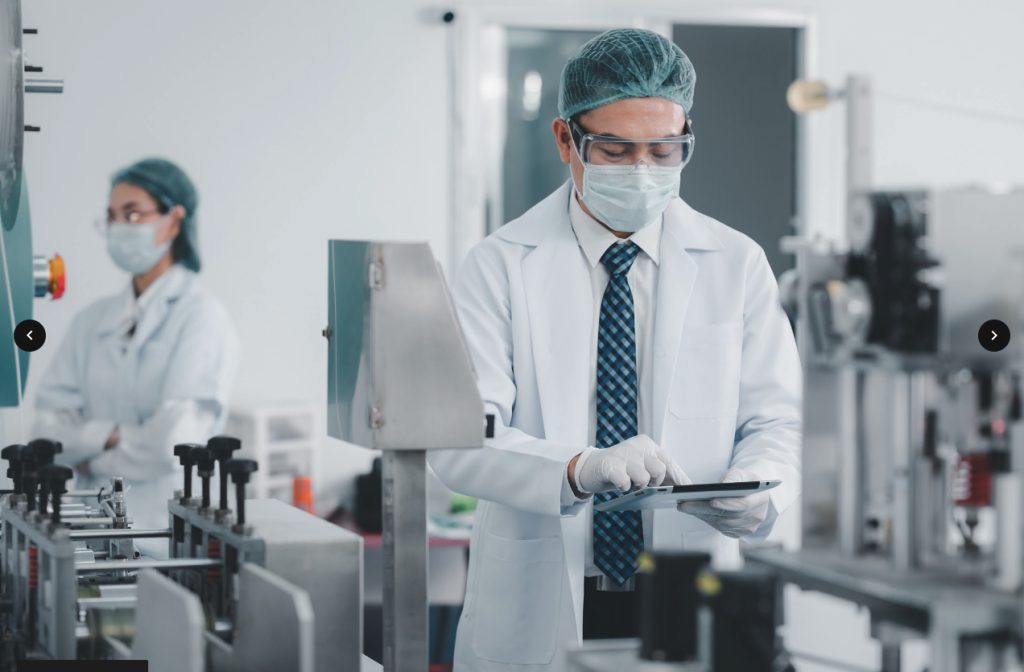
3. GMP-compliance – the baseline
GMP-compliance ensures that a pharmaceutical, cosmetic, or food product does not put users at risk, has consistent high quality, and is appropriate for its intended use.6
Good manufacturing practices (GMPs) are guidelines defined by the World Health Organization, with health authorities like the European Medicines Agency (EMA) or the Food and Drug Administration (FDA) in the U.S. having slightly altered requirements.
They are defined as the minimum standards that producers within the cosmetics, food, and pharmaceutical sector must meet in their production process.7 Among others, GMP guidelines can entail quality assessments, cleanroom environments, aseptic filling and packaging methods – to name but a few8.
By using automation in medical device manufacturing, it becomes easier to adhere to GMP requirements due to a minimized need for human intervention and reduced contamination risks. The ESSERT ADVANCED Robotic Workstation is designed to comply with GMP standards and can be operated in cleanrooms up to ISO class 5. It offers elevated protection from contamination and can be customized for aseptic fabrication.
4. Standardized processes and customizability – all but contrary
Standardized processes and customizability may seem like major opposites when it comes to manufacturing. However, this is not true when referring to HMLV production. Despite high-runner plants themselves often being tailor-made, standardized processes seem to be a feature reserved for high quantity productions, where consistency is key. However, the workflow of low volume, personalized productions can benefit from standardization as well.9
This can be achieved by reducing the amount of manual handling within production environments. With the help of standardized automation modules as part of a production chain, quality standards can be improved for the customized medical device industry with a higher level of compatibility. As specific production processes rely on different structures and requirements, flexible automation solutions are key for customized medical device companies.
In the quest for combining customizability with the benefits of standardized manufacturing, the ESSERT MicroFactory represents an answer for HMLV manufacturers. Each module takes over one step within a production process, and can easily be reconfigured, replaced, or complemented.
5. Flexibility when production lines are altered
Another important factor that distinguishes HMLV from mass productions is the need for flexibility. The different steps when manufacturing a medical device largely stay the same in mass productions. However, HMLV productions are subjected to constant changes based on customer demands.10
Production environments are regularly changed – e.g. from syringes to autoinjectors –, which means that when automated solutions are integrated in the process, they have to be easy to readjust. Consequently, it is essential that robotics are user-friendly in terms of assembly and mobility when it comes to smaller customized productions.
6. Scalability of automated solutions
Customized medical device production does not only rely on flexible solutions when it comes to the different steps of the production process. Another big consideration to be made is the aspect of scalability of automated solutions.
Especially in areas like biomanufacturing, but also in medical device manufacturing, production capacities have to be able to move quickly from test phases and clinical trials to scale-up and scale-out.11
Thus, another feature that makes automation platforms by ESSERT a preferred choice for HMLV manufacturers is their scalability that enables tests and studies to grow from lab to small-scale production and allows for a proper preparation for scale-up challenges: The ESSERT MicroFactory, consisting of multiple ADVANCED Robotic Workstations, can be adjusted by altering or adding individual modules, which may also be pre-validated for even faster transitions.
7. Autonomy, with room for manual interventions
Autonomy is another factor worth considering regarding automated medical device assembly, and one that must not be underestimated. Many companies offering medical device assembler jobs have difficulties to fill these positions, as workers with assembly experience and necessary education are often hard to come by.
Job descriptions for medical device assemblers typically include certifications like a high-school diploma. While several years of experience are often not necessary for entry-level jobs, assembly capabilities do come in useful and require some training.12
Automated medical device assembly has the potential to fill this gap in workforce and reduce downtime simultaneously, as machines can basically work full-time. At the same time, it is important that automated solutions leave the opportunity to interfere manually in some steps of the assembly process.
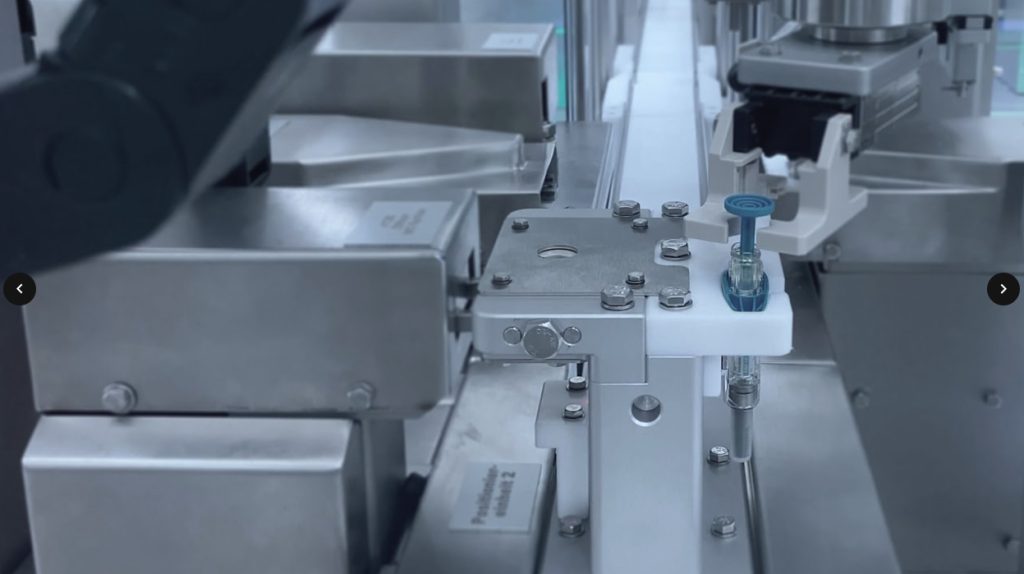
Getting the job done – with the ESSERT MicroFactory
HMLV medical device production comes with its own challenges, but also a lot of potential. Automated solutions by ESSERT Robotics are able to enhance the medical device assembly line, save time and ensure that baselines like GMP guidelines and sterile manufacturing environments are given.
The ESSERT MicroFactory consists of several process modules called ADVANCED Robotic Workstations, that are GMP-compliant and easily adaptable. Tasks that can be handled with ADVANCED Robotic workstations (on their own or in combination) range from syringe assembly to automated pipetting, medical device testing and the packaging of medical products.
They can easily be arranged in a way that fits your individual demands for successful medical device production. They allow for a high level of scalability, in case up-scaling and out-scaling is needed, as additional workstations can be added any time. The Process Control Center running ESSERT OS makes it possible to switch between recipes and produce multiple products within the ESSERT MicroFactory, powered by software-based changeovers.
With this automated medical device assembly line, the need for human intervention is reduced significantly, which means that process safety and sterilization management are easier to master. At the same time, reduced down-times lead to a decrease in costs and improve time efficiency, allowing to assemble medical devices more efficiently, GMP-compliant, and with elevated safety.
- Juan M. Jauregui Becker, Jesper Borst, Abele van der Veen. “Improving the overall equipment effectiveness in high-mix-low-volume manufacturing environments”.
CIRP Annals. Volume 64, Issue 1, 2015. Pages 419-422. DOI: https://doi.org/10.1016/j.cirp.2015.04.126. ↩︎ - Gan, Zhi Lon, Siti Nurmaya Musa, and Hwa Jen Yap. “A Review of the High-Mix, Low-Volume Manufacturing Industry.” Applied Sciences 13.3 (2023): 1687. ↩︎
- Ramstorp, Matts. Introduction to contamination control and cleanroom technology. John Wiley & Sons, 2008. ↩︎
- Whyte, William. Cleanroom technology: fundamentals of design, testing and operation. John Wiley & Sons, 2010. ↩︎
- “GMP cleanroom classification”. GMP Insiders. https://gmpinsiders.com/gmp-cleanroom-classifications/. Accessed: 05 March 2024. ↩︎
- “Good manufacturing practice”. European Medicines Agency. DOI: https://www.ema.europa.eu/en/human-regulatory-overview/research-and-development/compliance-research-and-development/good-manufacturing-practice#:~:text=Good%20manufacturing%20practice%20(GMP)%20describes,European%20Union%20(EU)%20level. Accessed: 04 March 2024. ↩︎
- “Good manufacturing practice”. European Medicines Agency. DOI: https://www.ema.europa.eu/en/human-regulatory-overview/research-and-development/compliance-research-and-development/good-manufacturing-practice#:~:text=Good%20manufacturing%20practice%20(GMP)%20describes,European%20Union%20(EU)%20level. Accessed: 04 March 2024. ↩︎
- “Medicines: Good manufacturing practices”. World Health Organization. DOI: https://www.who.int/news-room/questions-and-answers/item/medicines-good-manufacturing-processes#:~:text=What%20is%20GMP%3F,through%20testing%20the%20final%20product. Accessed: 05 March 2024. ↩︎
- Johansen, Kerstin, Sagar Rao, and Milad Ashourpour. “The role of automation in complexities of high-mix in low-volume production–a literature review.” Procedia CIRP 104 (2021): 1452-1457. ↩︎
- Gan, Zhi Lon, Siti Nurmaya Musa, and Hwa Jen Yap. “A Review of the High-Mix, Low-Volume Manufacturing Industry.” Applied Sciences 13.3 (2023): 1687. ↩︎
- Crater JS, Lievense JC. Scale-up of industrial microbial processes. FEMS Microbiol Lett. 2018 Jul 1;365(13):fny138. DOI: 10.1093/femsle/fny138. PMID: 29860483; PMCID: PMC5995164. ↩︎
- Indeed. How To Become a Medical Assembler in 5 Steps (Plus Salary). https://www.indeed.com/career-advice/finding-a-job/how-to-become-medical-assembler. 2022. ↩︎