Robots in Manufacturing: Revolutionizing Production Processes
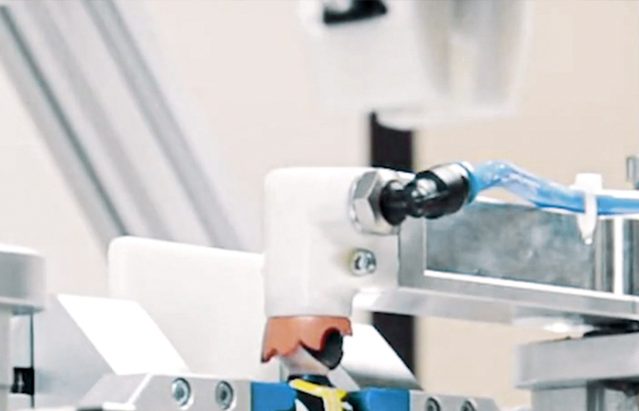
Robotic manufacturing refers to automated systems designed to perform tasks within the production processes of industrial facilities. Automation lies at the core of robotic systems in manufacturing. By leveraging industrial robots equipped with sensor technology or artificial intelligence, manufacturers can streamline their production processes, enhance productivity, and improve overall quality.
Robots are deployed across various stages, including material handling, assembly lines, and palletizing. Robots come in different configurations, ranging from traditional robotic arms to collaborative robots (cobots) designed to work alongside human operators. Additionally, the integration of Internet of Things (IoT) connectivity and vision systems enables robots to operate in real-time environments, facilitating efficient monitoring and control of production activities.
The evolution of manufacturing robots has been instrumental in driving the industrial revolution, particularly in sectors such as automotive, electronics, and aerospace. Early robotic systems, such as the first industrial robot introduced by Unimate in the 1960s, laid the foundation for modern robotics in manufacturing. Today, companies like Fanuc and Universal Robots continue to lead the way in developing cutting-edge robotic technology to meet the evolving needs of the manufacturing industry.
Types of Robotic Manufacturing
Various types of robotics are employed to address different production needs and challenges. Let’s explore the most common types of robotic manufacturing systems:
Industrial Robots
Industrial robots are typically fixed in place and are programmed to perform specific tasks with precision and repeatability. They are commonly found in automotive assembly lines, electronics manufacturing, and other industries requiring high levels of automation. Companies like Fanuc from Japan and ABB from Switzerland are renowned for their traditional industrial robot offerings.
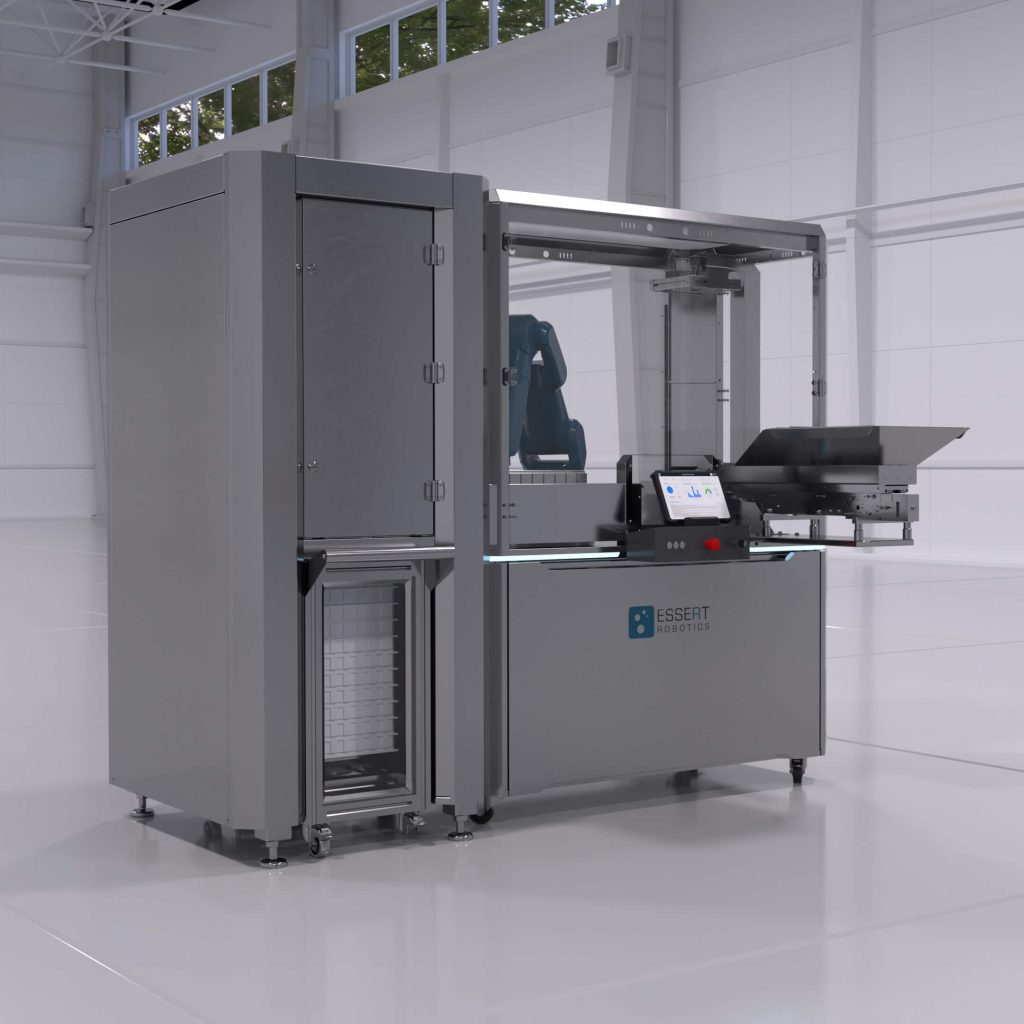
Collaborative Robots (Cobots)
Collaborative robots, or cobots, are designed to work alongside human operators in a shared workspace. Unlike traditional industrial robots, cobots are equipped with advanced safety features, such as force-limiting sensors and power-and-force limiting technology, allowing them to operate safely in close proximity to humans. Cobots are highly adaptable and can be easily reprogrammed to perform various tasks, making them ideal for small-batch production and agile manufacturing environments.
Autonomous Mobile Robots (AMRs)
Autonomous mobile robots (AMRs) are robotic platforms equipped with navigation systems, sensors, and onboard computers, enabling them to navigate autonomously in dynamic environments. These robots are commonly used for material transport and logistics applications within manufacturing facilities. AMRs offer flexibility and scalability, allowing manufacturers to optimize their internal logistics processes and improve overall operational efficiency.
Flexible Manufacturing Systems (FMS)
Flexible manufacturing systems (FMS) are integrated manufacturing systems consisting of various automated and semi-automated machines, robots, and computer-controlled processes. FMS allows for rapid changeovers and reconfigurations, enabling manufacturers to produce a wide range of products with minimal downtime. This approach emphasizes agility and responsiveness to changing market demands, making it well-suited for industries with high product variability and customization requirements.
At ESSERT Robotics, we focus on Industrial Robots and Flexible Manufacturing Systems. We install industrial robots in our movable workstation. The architecture and application of the ADVANCED Robotic Workstation allows flexible scaling and application for different product variants.
Machine Learning and Artificial Intelligence (AI)
In the future, all described types of robots benefit from machine learning and artificial intelligence (AI). These systems are optimizing robotic manufacturing by enabling robots to learn from data, adapt to changing environments, and make intelligent decisions in real-time. Furthermore, integrated vision systems, such as cameras and image processing algorithms, enable visual perception and feedback.
These technologies empower robots to optimize production processes, predict maintenance needs, and identify opportunities for improvement. By leveraging AI-driven insights, manufacturers can enhance productivity, reduce costs, and drive innovation in their operations.
Mass production vs. flexible manufacturing
Two primary strategies for automation are often employed: mass production and flexible manufacturing. These approaches differ significantly in their focus, adaptability, and application within industrial settings. Let’s explore the requirements in manufacturing automation between mass production and flexible manufacturing:
Mass Production
Mass production is a manufacturing strategy centered around the efficient production of large quantities of standardized products. It typically involves the utilization of automated production lines configured for high-volume output at high-speed. Mass production is characterized by its emphasis on uniformity, predictability, and economies of scale. This approach is well-suited for industries where product demand is stable, and there is a consistent need for large quantities of identical goods.
Flexible Manufacturing
Flexible manufacturing, on the other hand, prioritizes adaptability, versatility, and responsiveness in production processes. This approach is designed to accommodate variations in product design, demand, and customization requirements. Flexible manufacturing systems utilize advanced automation technologies, such as robotic arms, CNC machines, and computer-controlled equipment, to enable rapid reconfiguration and reprogramming of manufacturing operations. This flexibility allows manufacturers to quickly adjust production schedules, change product specifications, and efficiently handle small-batch production runs.
In regard to flexible manufacturing in the robotics industry, ESSERT Robotics stands out with its innovative ADVANCED Robotic Workstation. At ESSERT Robotics we integrate cutting-edge technologies, including robotic arms, sensor technology, and components from renowned robotic manufacturers, into a versatile and mobile automated workstation. The ADVANCED Robotic Workstation is designed to adapt seamlessly to varying production needs, enabling the production of a wide range of products with efficiency and precision.
One notable feature is the possibility to combine multiple workstations to create an ESSERT MicroFactory, a productine line for High Mix / Low Volume requirements. The modular architecture allows for easy customization and reconfiguration of production setups with just a few software clicks.
Applications of Robots in Manufacturing
Robots are integral to modern manufacturing, facilitating diverse applications such as palletizing, quality control, material handling, assembly, and more. They enhance productivity, ensure product quality, and optimize operational efficiency, contributing to the success and competitiveness of manufacturing industries worldwide. The industries range from food and beverages to pharmaceuticals, electronics, and automotive industry.
Typical robotic applications include:
- Palletizing
- Quality Control
- Material Handling
- Assembly
- Dangerous Task Handling
- CNC Machining
- Pick-and-Place Operations
- Welding and Soldering
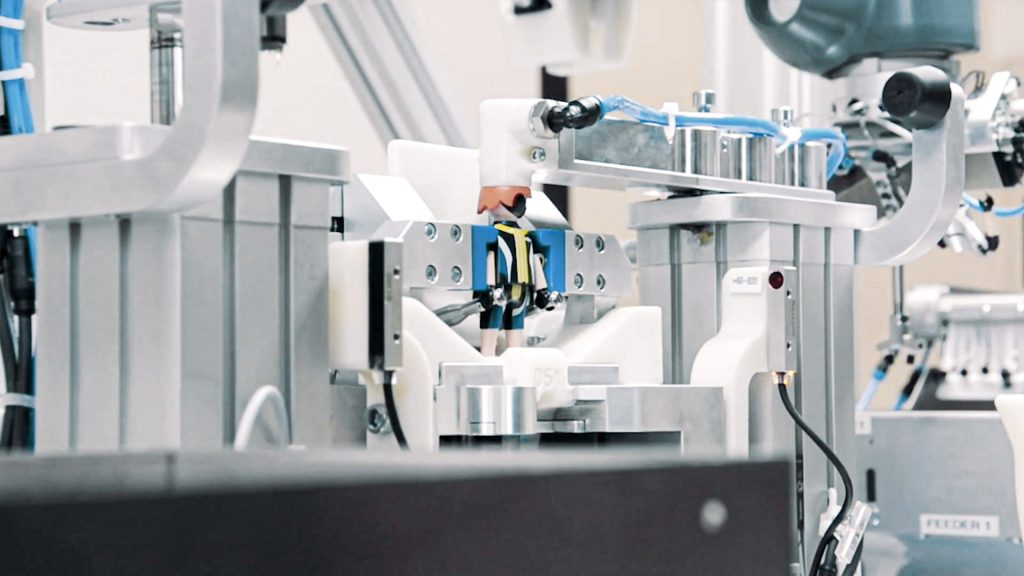
Advantages of Robotic Manufacturing
By leveraging robotic automation, companies can streamline production processes and stay competitive in today’s dynamic market. Some key advantages include:
- Cost Savings: Implementing robots in manufacturing leads to significant cost savings over time. While the initial investment may be substantial, robots reduce labor costs in the long run by increasing productivity and efficiency.
- Increased Productivity: Robots are capable of working tirelessly and with precision, resulting in higher productivity levels compared to human workers. They can operate 24/7 without fatigue, leading to enhanced output and shorter production cycles.
- Improved Safety: Robots can perform dangerous tasks with precision and reliability, reducing the risk of workplace accidents and injuries. By automating operations in laboratories or pharmaceutical manufacturing, producers create safer working environments for employees.
- Enhanced Product Quality: Robots ensure consistency and accuracy in manufacturing processes, leading to improved product quality and reliability. They minimize errors and deviations, resulting in fewer defects and higher customer satisfaction.
- Flexibility and Adaptability (for flexible automation systems): Flexible manufacturing automation systems enable quick reconfiguration and adaptation to changing production needs. This agility allows manufacturers to respond swiftly to market demands, introduce new products, and optimize production schedules.
Considerations of Robots in Manufacturing
When integrating robots into manufacturing processes, several critical considerations must be taken into account to ensure successful implementation and operation.
- Initial Investment Costs: Companies must assess the upfront costs of purchasing, installing, and integrating robotic systems.
- Downtime and Workflow Disruptions: Potential disruptions during integration necessitate thorough planning and contingency measures to minimize impact.
- Training and Maintenance: Proper training and proactive maintenance are essential to ensure safe and efficient operation of robotic equipment.
While the adoption of robots in manufacturing offers significant benefits such as increased productivity, cost savings, and improved product quality, it also presents challenges that must be carefully navigated. With proper planning, strategic investment, and a focus on continuous improvement, manufacturers can position themselves for long-term success and growth in an increasingly automated world.
Outlook to the future of manufacturing
As we look to the future, the role of robots in manufacturing is poised for continued growth and innovation. With advancements in technology, including machine learning, artificial intelligence, and Industry 4.0 integration, the capabilities of robotic systems are expected to expand further. Predictions suggest that automation will play an increasingly integral role in streamlining production processes, enhancing efficiency, and driving economic growth in the manufacturing industry.
However, as automation becomes more prevalent in manufacturing, ethical considerations surrounding the use of robots must be carefully evaluated. Questions about the ethical implications of autonomous decision-making, worker safety, and data privacy in robotic systems require thoughtful consideration and regulation to ensure responsible deployment and use of technology.
International organizations like the International Federation of Robotics (IFR) play a vital role in shaping the future of robotics in manufacturing. The IFR provides guidance, standards, and advocacy to ensure the responsible development and deployment of robotic technology.
Robotic manufacturing with ESSERT Robotics
ESSERT Robotics offers innovative solutions to enhance efficiency and flexibility in manufacturing processes. Leveraging robotic technology and modular architecture to address the evolving needs of modern manufacturing, we have developed the ADVANCED Robotic Workstation.
Our flexible automation solution enables seamless adaptation to changing production requirements, while our emphasis on ease of use in setup and changeovers opens the door to manufacturing automation for companies across various industries and production volumes.
FAQs about Robots in Manufacturing
What are robotic arms?
What is the most common manufacturing robot?
What is an articulated robot?
How are robots changing manufacturing?
Read more about robotics
Robotic manufacturing companies
Cobot – all you need to know about collaborative robots
What is an industrial robot?
Robotics in the pharmaceutical industry
Robotics – 7 facts you need to know