Cobot – all you need to know about collaborative robots
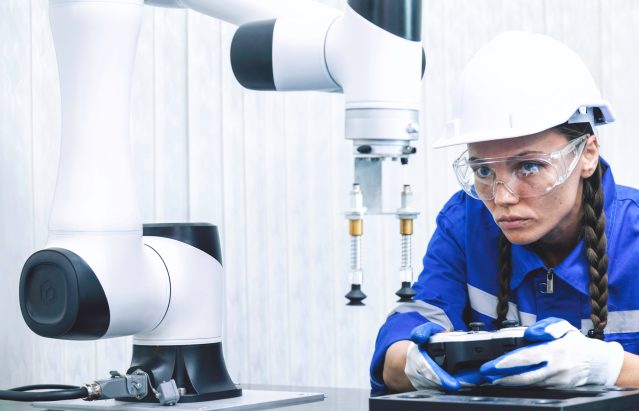
In recent years, the landscape of industrial automation has been reshaped by the emergence of collaborative robots, commonly known as cobots. These innovative machines represent a significant advancement in robotics, offering a unique blend of automation and human interaction.
Cobots are designed to work in sync with human workers. With their ability to automate repetitive tasks while ensuring safety and efficiency, cobots have quickly become integral components of modern industrial settings.
In this article, we will cover some essential aspects of the wide area of cobots, including some basic information as well as benefits and applications of cobots.
What is a cobot?
A cobot is a collaborative robot designed to work alongside human operators in a shared workspace. Unlike traditional industrial robots, cobots are optimized for physically interacting with humans.1
Cobots may feature adaptable robot arms capable of handling various payloads. With customized end-effectors, they excel in specific robot applications across diverse industries. These machines prioritize human-robot collaboration, automating repetitive tasks to enhance overall efficiency in the work environment.
Cobot or industrial robot: The differences
Comparing collaborative robots (cobots) and industrial robots reveals critical differences. Traditional industrial robots operate autonomously in isolated settings. Typically, industrial robots are not designed to allow human interaction, as they do not feature the required safety technologies. They are optimized for manufacturing environments, such as in the automotive or in the pharmaceutical industry.
In contrast to robots, cobots open up a new level of collaboration, as they are designed to work alongside human counterparts, requiring both safety features and adaptability.
Benefits of collaborative robots
There are several benefits of cobots that their implementation brings in various applications, most of all in industrial settings. Cobots boast versatile payload capacities, making them adaptable to a wide range of applications. Their user-friendly design ensures easy integration into workflows, enhancing overall efficiency.
The main – and most obvious – benefit of cobots is based on how cobots work alongside humans. The collaboration between human workers and cobots significantly influences product quality, especially in tasks requiring precision and stringent quality control along with versatility. Cobots may take over routine operations or fields where human capabilities in terms of strength, precision, or efficiency no longer suffice. This allows human workers to focus on more complex tasks, ultimately making the entire process cost-effective.
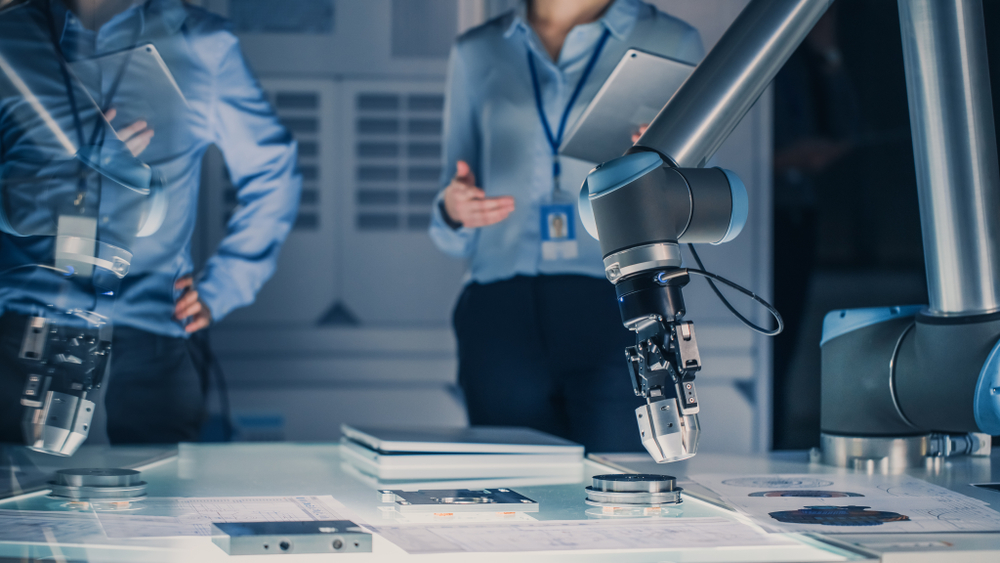
Regulations concerning cobots – what to bear in mind
Incorporating collaborative robots into the workplace necessitates adherence to specific regulations ensuring safety and ethical standards. Key regulations include:
- ISO 10218 and ISO 15066: Globally recognized ISO standards outlining safety requirements for industrial robots, ensuring cobots adhere to established safety norms.
- ANSI/RIA R15.06-2012: An American National Standards Institute standard offering guidelines for the design, use, and safe integration of industrial robots, including collaborative systems.
- OSHA Regulations (USA): Occupational Safety and Health Administration regulations in the United States outline employer responsibilities for ensuring a safe workplace, including cobot integration.
- ISO 13849-1 and ISO 13849-2: International standards focusing on safety-related parts of control systems, providing criteria for designing and implementing safety systems in cobots.
Example – how can a cobot collaborate with workers?
A cobot, or collaborative robot, is designed to work together with human operators, prioritizing safety and adaptability. They’re versatile, easily reprogrammable, and equipped with various end-effectors for specific tasks.
In inventory management, for instance, cobots autonomously handle material, support assembly lines, and perform quality inspections. Leveraging advanced algorithms, they analyze data for decision-making, ensuring accurate stock levels. Armed with intricate sensors, these robots exhibit an acute awareness of shared workspaces, adeptly navigating alongside human counterparts by dynamically adjusting their movements.
However, by far not all cobots are meant to be mobile: In areas like manufacturing, robots made for collaboration are often designed as static systems with room for a manual operator to either control the robot or take on an active role in the manufacturing process.
Cobots in manufacturing
Cobots have revolutionized manufacturing processes, enhancing efficiency and precision across various tasks. In assembly, they work alongside humans, seamlessly constructing intricate components. Their adeptness extends to pick-and-place operations, efficiently handling items with precision.
Quality control is another forte, as cobots meticulously inspect products to ensure stringent standards are met. Versatile end-effectors enable them to execute tasks with accuracy, from gripping to specialized tool usage. Acting as sophisticated manipulators, cobots navigate complex production setups, optimizing outcomes.
Applications – cobots across various industries
Cobots find a variety of applications across different industries; key areas of cobot applications include:
- Rehabilitation: Cobots are finding applications in rehabilitation processes, supporting physical therapy for patients. Their adaptive nature allows them to work in tandem with therapists, providing targeted assistance for rehabilitation exercises.
- Automotive Industry: Cobots are integral components of production lines in the automotive industry, performing tasks like palletizing, machine tending, material handling, and assembly line support with high repeatability.
- Logistics: Cobots play a pivotal role in logistics, especially in tasks like material handling, packing, and order fulfillment.
- Aerospace: Cobots are utilized in aerospace industries for tasks such as part assembly, inspection, and material handling in complex production environments.
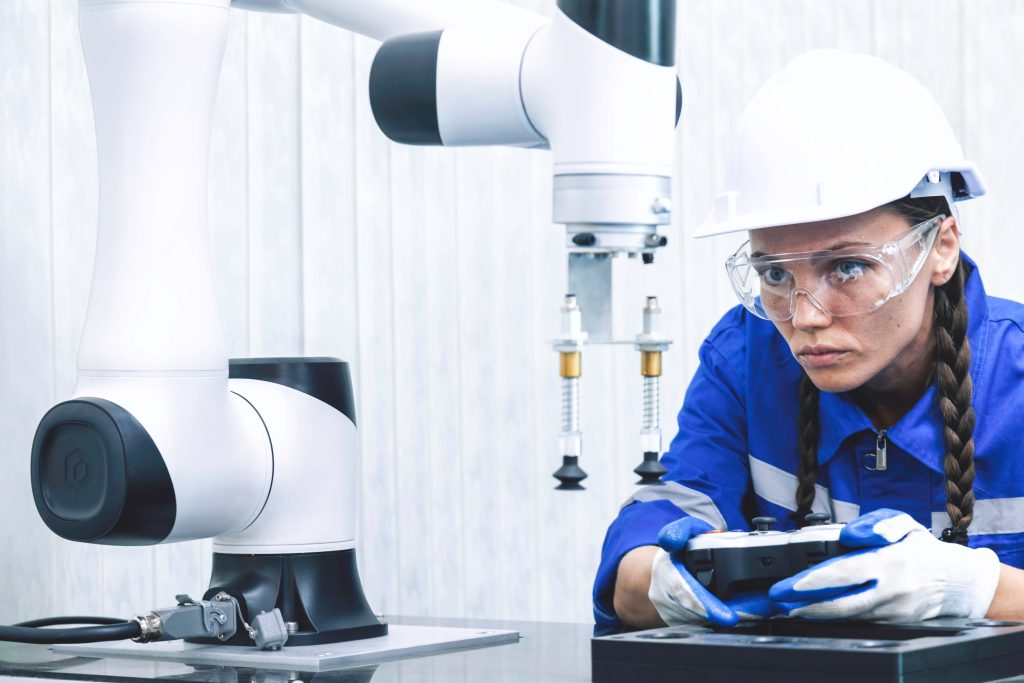
Downsides of cobots – where industrial robots are preferred
Despite their transformative impact on industrial automation, cobots have limitations in comparison to industrial robots. Cobots, designed for collaboration with humans, may not be entirely autonomous, requiring more human intervention in programming, handling, and task supervision. This characteristic can make them less efficient in environments with high mix/low volume (HMLV) production, where traditional robots often prove more effective in handling diverse tasks, reducing downtimes and enhancing the level of traceability.
Moreover, cobots may not be ideal in environments where human presence is undesirable, such as in dangerous settings or specific pharmaceutical applications, where stringent contamination control is crucial. Industrial robots, with their capacity for complete autonomy and absence of reliance on human interaction, are often preferred in such scenarios. This highlights the importance of choosing the right robotic solution based on the specific requirements of the task or industry.
Collaborative robots by ESSERT Robotics
ESSERT Robotics pioneers robotic solutions by offering state-of-the-art systems like the ADVANCED Robotic Workstation and MicroFactory. These systems revolutionize fields like pharmaceutical production or laboratory processes, allowing (but not requiring) the integration with human operators and adapting to dynamic production needs.
The ADVANCED Robotic Workstation is a flexible and scalable robotic solution, suitable for numerous tasks with a high level of autonomy. It is cGMP-compliant and ready to be used in clean rooms up to ISO class 5.
Meanwhile, the MicroFactory provides a modular production line that allows human-robot interaction as well. Composed of multiple Robotic Workstations, modules can be individually customized and also pre-validated in order to further increase the flexibility of pharmaceutical processes powered by robots.
Read more about robotics
Robots in manufacturing: revolutionizing production processes
Robotic manufacturing companies
What is an industrial robot?
Robotics in the pharmaceutical industry
Robotics – 7 facts you need to know
- Cobots: Robots for collaboration with people. 2/20https://peshkin.mech.northwestern.edu/cobot/ ↩︎