Material separation in the pharmaceutical industry
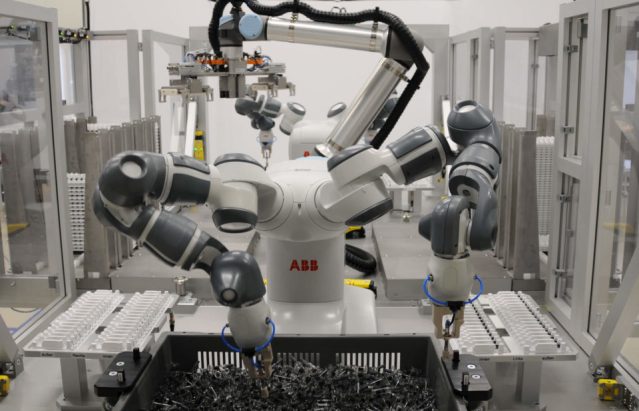
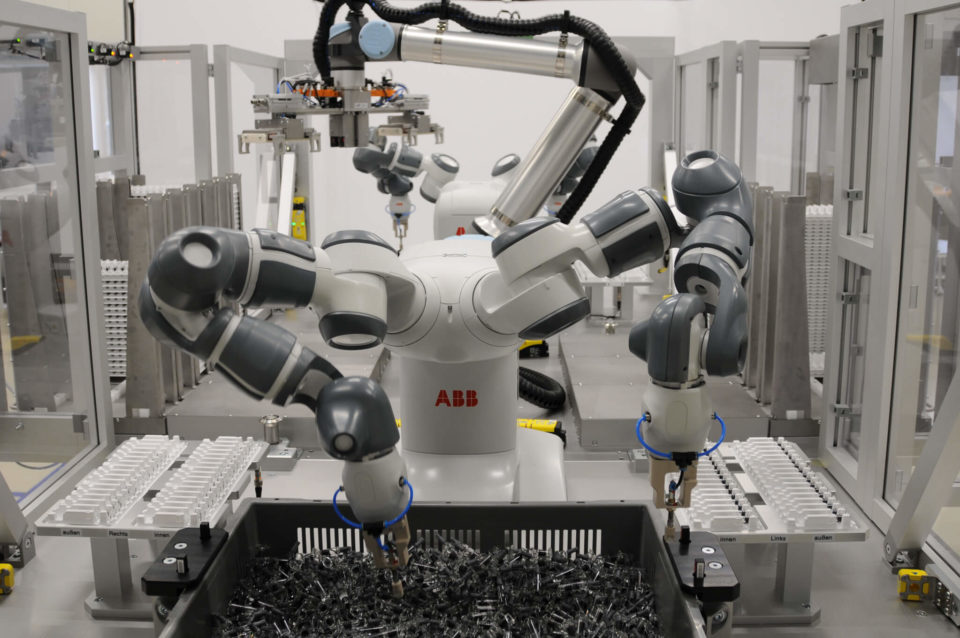
The trend towards smaller batch sizes and shorter product life cycles is not stopping in the pharmaceutical industry. Although there are still the large high-runner products, more and more specialized drugs for smaller target groups are also being offered on the markets in parallel.
These are developed by small biotech companies, among others, which rarely operate their own production facilities and then have these active ingredients filled and refined on a contract basis. This trend is lucrative, but it poses new challenges for conventional production, packaging, labeling and quality control of the drug products.
While the so-called blockbuster products can often be manufactured for years on the same production lines in a fully automated manufacturing process, pharmaceutical companies have recently become dependent on flexible solutions with rapid product and packaging changes. This requires a rethinking of production processes and thus also a change in pharmaceutical production technology. Whereas with large batch sizes it was often the machine downtimes caused by malfunctions or maintenance, changeover times and product, batch and format changes now also play a defining role.
Material separation as a production step
ESSERT Robotics has taken up this challenge in a process step. An important sub-process in the manufacture of medicines is the separation of materials for further processing.
This still works relatively easily with tablet blisters or rectangular drug packages.
However, when it comes to transparent syringe barrels, for example, which are delivered in containers or crates as bulk goods, employees are often still on duty who have to transfer the syringes manually into trays provided.
The manual intervention of humans within the manufacturing process should be reduced to a minimum, especially for medical devices.
The solution: Speed Bin Picking
The so-called speed bin picking method, which was specially developed by ESSERT Robotics for the process step described, enables fast cycle times, high quality requirements, and flexible and simple changeover of the products. For example, in order to remove syringes from the containers quickly and efficiently for further processing, four important factors are crucial for a safe process.
Factor #1: The material recognition
Here, ESSERT Robotics relies on the latest innovative 3D vision technology with specially developed evaluation algorithms.
With the help of the fringe projection method, the camera sensor used is able to record three-dimensional images. These are needed for the second important factor – the robot.
Factor #2: The robot
The 3D camera detects the material and sends the robot the exact position coordinates of the syringe detected and to be gripped.
In order to meet the high cycle time, ESSERT relies on a two-arm robot that is able to grip in parallel and thus twice as fast in a humanoid process that is very similar to humans.
Factor #3: Grasping
Thanks to a pneumatic suction gripper, safe gripping of the syringes can be ensured and glass-to-glass contact avoided, thus meeting the high quality requirements in the process.
Factor #4: Tray handling
With the aid of one or more additional integrated tray handling stations, full trays can be discharged from the system and empty trays made available.
This allows a flexible response to the cycle time and the batch to be produced. In addition, an autonomy time of over 1.5 hours can be guaranteed.
The product changeover works at the push of a button. Thanks to preset product types and easy-to-configure program templates, different formats of glass syringes can be separated on the system.
For maximum flexibility, ESSERT Robotics offers a modular platform system. Additional modules can be docked onto the speed bin picking system easily and uncomplicatedly, thus expanding the production capacity.
n contrast to a classic palletizer, a solution has been created that allows different trays to be handled through simple moldings.
Due to a large number of tray magazines and safe handling, it is possible to load and unload trays during the running process by means of a drawer principle.