High Mix / Low Volume: Possibilities & Limitations
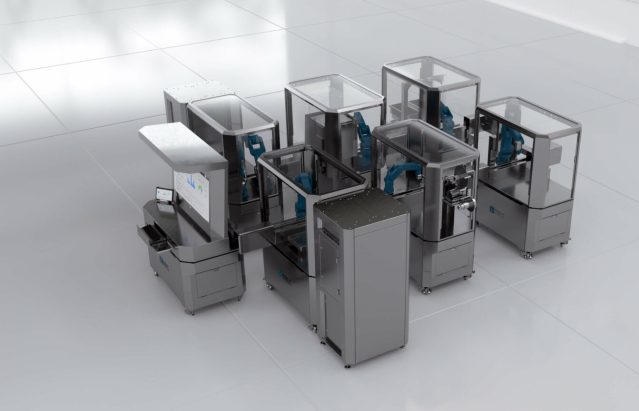
High Mix / Low Volume is an increasingly prominent production approach in the pharmaceutical sector. This correlates with the rise of advanced therapies that are custom-made for a small group of individuals – or even one single patient.
Personalized therapies have allowed huge leaps in the treatment of several severe diseases, but they come with challenges. And a price tag. Efficient High Mix / Low Volume production is therefore essential to streamline workflows, speed up lead times, enhance cost-effectiveness and reduce manufacturing costs in order to make custom-made products more accessible to the public.
High Mix / Low Volume manufacturing vs. Low Mix / High Volume manufacturing
The choice between Low Mix / High Volume (LMHV) and High Mix / Low Volume (HMLV) production strategies carries substantial implications. These strategies represent opposing approaches in manufacturing and depend on multiple factors – from the number of different products required to supply chain reliability and requirements related to geographic and logistic circumstances.
What is Low Mix / High Volume manufacturing?
Simply put, Low Mix / High Volume (LMHV) manufacturing revolves around mass production. It entails the production of large quantities of standardized products with minimal variations, with quantities of 100 and more units being produced per minute.
LMHV facilities prioritize efficiency and cost reduction through economies of scale, but are often less effective when it comes to alterations within manufacturing processes. Nevertheless, LMHV manufacturing usually relies on fewer, yet large machines that cannot be easily adapted.
What is High Mix / Low Volume manufacturing?
In contrast, High Mix / Low Volume (HMLV) manufacturing caters to diverse product variations in small quantities. Therefore, it is also referred to as make-to-order manufacturing. It emphasizes customization over mass production and usually results in smaller amounts of produced goods, often around 15 units per minute. On the other hand, HMLV manufacturing offers the flexibility to swiftly adapt to changing customer requirements and regulatory demands, as well as supply chain variations.
Read more: Low volume manufacturing vs. high volume manufacturing
High Mix / Low Volume manufacturing – whose business is it?
High Mix / Low Volume manufacturing is an increasingly popular approach in several branches – from the electronics and stationery industry to medical device production. Be it the ultrasonic welding of various small parts or the assembly of syringes containing high-priced drug substances – all over the world, there is a growing demand for customized products in smaller quantities, but with no quality leeway.
One of the sectors to which High Mix / Low Volume production can be considered defining is the personalized medicine market. Medical achievements in the field of advanced therapies, such as targeted cancer treatments or novel gene therapy approaches, are often exclusively produced for one individual.
This drives costs for these therapeutic approaches, which nonetheless keep shaping the pharmaceutical industry. Nevertheless, the personalized medicine market was estimated to be globally worth USD 538.93 billion in 2022, with an annual growth rate of 7.2 % projected until 20301.
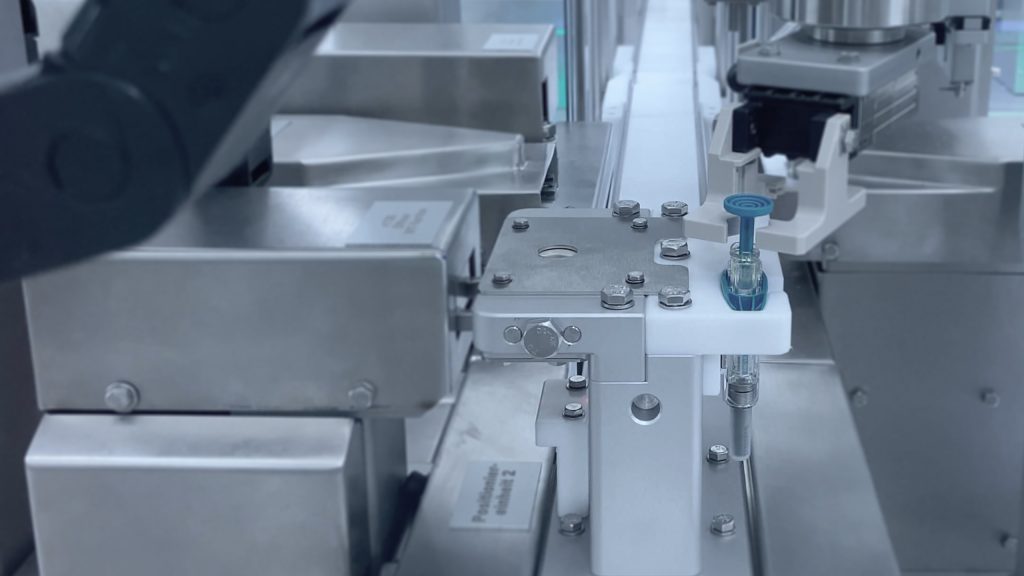
However, HMLV manufacturing is not only essential for the pharma industry, but also satisfies the growing, cross-branch need for decentralized processes: Products are increasingly being manufactured at different locations to gain more autonomy over supply chains, but also to adapt them more easily to a multitude of different markets and their individual requirements, e.g. in terms of secondary packaging of liquid drug products or the instruction leaflet.
To make a long story short: High Mix / Low Volume manufacturing is getting central to more and more branches, and is soon to become ubiquitous.
Possibilities of High Mix / Low Volume production
As already stated, HMLV production is becoming an increasingly adopted manufacturing approach by several markets, with the pharma industry being one of the sectors to make use of its unique advantages.
In the following chapters, we will shed light on the most convincing possibilities of HMLV manufacturing.
High level of customization in manufacturing
Especially in the pharmaceutical manufacturing processes, it is essential to tailor products to meet specific customer demands. Unlike mass production, which focuses on standardized items produced in large quantities, HMLV is all about catering to unique requirements.
This is true for fields like personalized medicine, where drug products are developed for only a few numbers of applications and are therefore individually produced on demand. However, the need for customization in the pharmaceutical sector reaches way further.
The “c” in “cGMP” already gives a hint on what is inherent to the pharmaceutical sector: variability. Whenever there are adaptations in, for instance, current Good Manufacturing Practices or other standards applying to a specific drug product, the manufacturer’s response to this alteration is crucial in maintaining approval.
Flexibility on supply chain changes
Flexibility on supply chain alterations is a critical aspect of High Mix / Low Volume (HMLV) manufacturing. It allows a smooth and efficient flow of production processes while accommodating a wide variety of products and responding effectively to disruptions. HMLV manufacturing systems are designed to achieve this flexibility.
The supply chain must satisfy the unique demands of a specific HMLV manufacturing process – disruptions can have a significant impact. But flexible production workflows in High Mix / Low Volume environments are able to handle unexpected challenges and maintain the production flow. This is because, per definition, HMLV manufacturing is laid out to allow maximum variability, be it in changing batch sizes or the substitution of a work piece no longer available.
One way HMLV manufacturing can increase supply chain independence is decentralized manufacturing – as discussed in the next section.
Decentralized manufacturing and late-stage customization
In recent years, pandemics, wars and other crises have demonstrated the fragility of global supply chains. This has led manufacturers to rely on smaller, but more independent production sites at different locations, where the entire manufacturing process is carried out at a smaller scale, but is also more resilient.
However, decentralized manufacturing does not necessarily imply the entire production process of a globally traded product to be carried out all over the world. Late-stage customization describes adaptations of finished or almost finished products destined for a specific market. These final steps of customization are frequently carried out directly in the target region, where, yet again, HMLV processes can play out their strengths. They allow a great variety of different products – be it luxury goods or drug products – to be efficiently customized to regional markets.
Advantages of HMLV in an overview
To sum up, HMLV brings several advantages over traditional manufacturing approaches. And they are not limited to the manufacturer, but extend to the customers and end consumers. The main advantages of High Mix / Low Volume production are:
- increased customizability of processes according to the customer
- agile production, able to adapt to changes and disruptions of supply chains
- possibility to decentralize production processes for advanced supply chain independence and adaptation to country-specific requirements
- increased space efficiency within manufacturing sites
- facilitated late-stage customization for a wide array of products
Challenges in HMLV processes
While High Mix / Low Volume (HMLV) production brings numerous opportunities, it also presents certain challenges that manufacturers must address, such as increasingly complex production processes and cost-efficiency.
Complex processes with challenges for staff
For pharmaceutical companies, the ability to adapt to rapidly changing production settings is vital. This requires implementing efficient methodologies to facilitate quick changeovers, minimize cycle time, and meet the dynamic demands of various manufacturing industries.
The introduction of new products as well as frequently changing production workflows make HMLV processes not only complex, but also challenging for staff – e.g. in changing routings, substituting raw materials or implementing new quality control measures within an assembly line.
In order to provide maximum process consistency and transparency, precise documentation of manufacturing operations is crucial. Still, the more complex the procedure, the more laborious gets the ongoing documentation for manufacturing companies. Therefore, automated systems are being increasingly adopted in HMLV production environments, allowing real-time process monitoring as well as regulatory compliance, meticulous quality control and documentation.
Cost-efficiency in HMLV manufacturing
Cost-efficiency is a fundamental challenge in the HMLV sector. It involves optimizing various aspects of production to ensure that resources are used in the most cost-effective manner possible.
The main aspect in terms of efficiency and costs are the challenges associated with changeover processes. Fast and flexible changeover processes without major technical measures must be aimed for in order to keep production downtime low and avoid costly rebuilds.
Furthermore, manufacturers aim to balance production quantities with demand, avoiding overproduction and the associated costs of excess inventory. One approach is to employ lean manufacturing principles to enhance cost-efficiency. This focuses on eliminating waste, reducing excess inventory, and streamlining production processes.
Production scheduling is another critical aspect. Efficient production scheduling in HMLV manufacturing ensures that resources are allocated effectively, reducing bottlenecks and preventing overproduction. This adaptability is crucial in a constantly changing type of production.
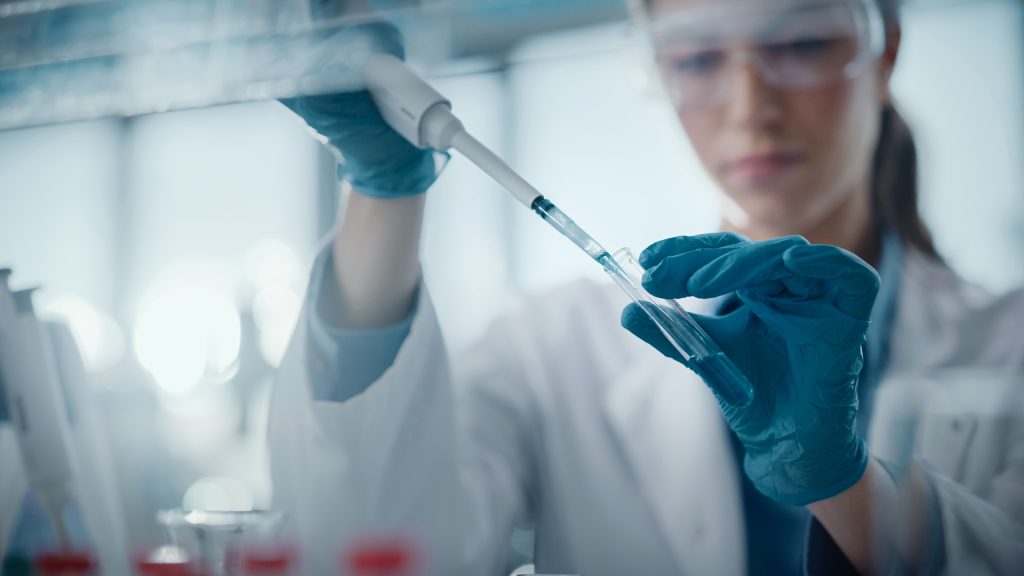
However, one of the most cost-intense aspects of HMLV production is personnel. Costs for specially trained staff come with great variations and become even more unpredictable due to world-wide shifts on the job markets. This shift is also accelerated by demographic changes, resulting in fewer qualified workers available to produce pharmaceutical products for an aging, thus growing group of customers.
These factors make it difficult for manufacturers to scale production on the one hand, and to maintain profitability along the entire production line on the other. Efficient manufacturing requires re-designed processes with a special focus on scalability and costs. One way to achieve this is to implement automated solutions that can work independently and therefore expand the production capacity. Additionally, automation can bring a higher level of consistency to production processes, reducing the risk of human error and related costs.
Improving efficiency in High Mix / Low Volume manufacturing with automated systems
Automation emerges as the linchpin in overcoming the challenges presented by High Mix / Low Volume (HMLV) manufacturing. It addresses the complexities of rapidly changing production settings by streamlining processes and enabling quick changeovers by the means of modular setups.
Read more: How to improve efficiency in High Mix / Low Volume manufacturing?
Automation also optimizes cost-efficiency by reducing labor costs and freeing up resources for those aspects of production they are most needed in. Furthermore, automated systems ensure compliance with regulatory standards and enhance data transparency. They can monitor and record production processes meticulously, providing traceability and accountability that align with industry-specific regulations.
In addition, with the option to pre-validate individual process steps rather than the entire production workflow over and over again, modular automation systems like the ESSERT MicroFactory help to maintain stringent production timelines. Modularity is also the buzzword for easy scalability. A modular automation solution is able to be flexibly expanded with increased production output.
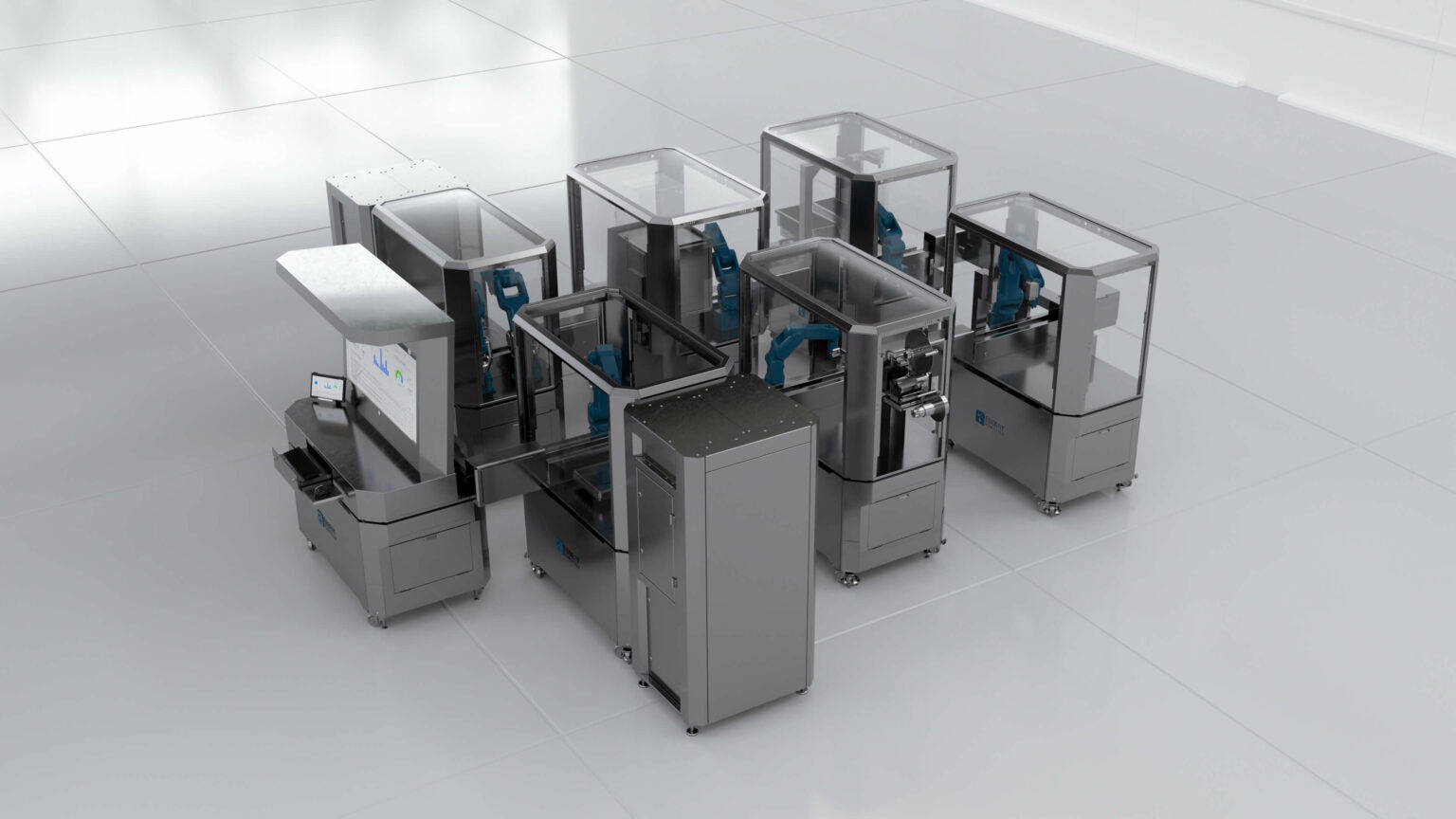
HMLV production – tailor-made automation with ESSERT Robotics
HMLV production is all about customization. So why should the manufacturing solutions themselves not be customized to HMLV manufacturers?
In fact, ESSERT Robotics provides solutions that fill this very gap: The ADVANCED Robotic Workstation is a fully automated platform offering functionality, ease of use, and the ability to handle various assembly modules. This streamlines production processes, reduces cycle times as well as production costs, and enhances throughput.
It comes with the ability to teach in new “future products” directly at the manufacturing site, with no informatic skills necessary and without the remaining production workflow being affected. This makes it highly customizable in order to automate redundant yet crucial production steps – easy scalability guaranteed, from lab applications all the way down to the commercialization of high-value products.
This is where the ESSERT MicroFactory comes into play: It consists of multiple Robotic Workstations and enables the entire production processes to be carried out autonomously and accurately, allowing the assembly of 15 to 20 pieces per minute. The option to pre-validate individual production steps to be seamlessly integrated in the existing workflow pays tribute to the need for flexible processes and helps manufacturers cope with demanding circumstances on a changing market.
In addition, with the option to pre-validate individual process steps rather than the entire production workflow over and over again, modular automation systems like the ESSERT MicroFactory help to maintain stringent production timelines. Modularity is also the buzzword for easy scalability. A modular automation solution is able to be flexibly expanded with increased production output.
FAQs
What is the difference between High Mix / Low Volume and Low Mix / High Volume?
How do you manage High Mix / Low Volume manufacturing?
What is an example of HMLV?
What are the challenges of High Mix / Low Volume?
What is the typical output of High Mix / Low Volume manufacturing?
- Personalized Medicine Market Size, Share & Trends Analysis Report By Product (Personalized Medicine Therapeutics, Personalized Medical Care, Personalized Nutrition & Wellness), By Region, And Segment Forecasts, 2023 – 2030. https://www.grandviewresearch.com/industry-analysis/personalized-medicine-market (9/21/2023). ↩︎