Cobot vs. robot – what sets them apart?
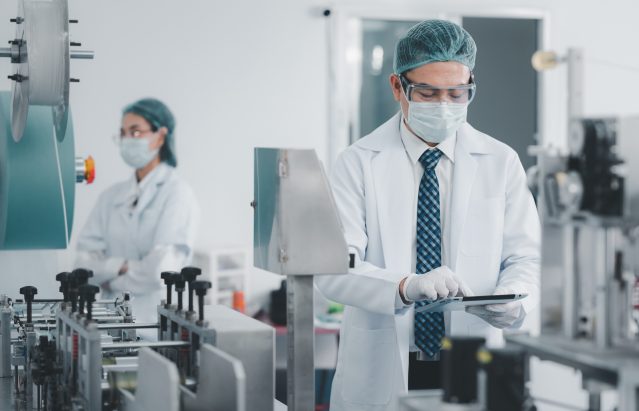
With the increasing integration of robotics into industrial and pharmaceutical processes, distinguishing between traditional industrial robots and cobots has become essential. Apart from several similarities, these two types of robots serve distinct purposes and offer unique advantages in various manufacturing environments.
In this article, we will explore the differences and similarities between cobots and robots, shedding light on these exciting representatives of robotics.
Definition – industrial robots
Industrial robots are automated machines designed to perform industrial work with precision and efficiency. These robots are typically programmed to carry out repetitive tasks in manufacturing processes, ranging from assembly and welding to material handling and packaging.
Industrial robots are characterized by their ability to operate autonomously, following programmed instructions to execute tasks with accuracy and speed. They play a crucial role in streamlining production processes, improving productivity, and enhancing the quality of manufactured goods.1
Definition – collaborative robots
Collaborative robots, commonly referred to as cobots, represent a type of robot specifically designed to work alongside humans. Cobots are engineered with advanced safety features and sensors that allow them to operate safely in proximity to human workers.2
The primary objective of collaborative robots is to enhance efficiency and productivity by facilitating a harmonious interaction between humans and machines, combining their individual strengths. Hence, these robots are characterized by their ability to adapt to dynamic environments.
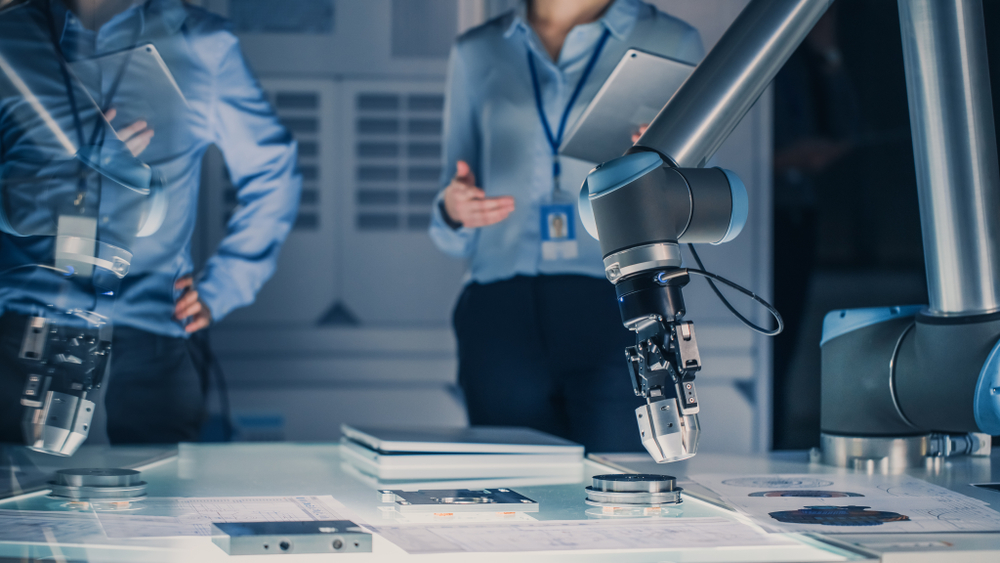
Similarities of cobots and robots
Both collaborative robots (cobots) and traditional industrial robots share several common characteristics, contributing to their role in revolutionizing manufacturing and automating manual processes:
Automation capabilities: Cobots and robots are equipped with automation capabilities, enabling them to carry out tasks with high uniformity and efficiency. This automation is essential for streamlining production workflows and reducing manual labor.
Precision: Both types of robots exhibit high levels of precision in their movements and actions. This precision is crucial for tasks that require accuracy, such as assembly, welding, or material handling, ensuring consistent and top-notch results.
Reliability: Cobots and industrial robots are designed to operate reliably in various settings. Their consistent performance is vital for meeting production targets and maintaining overall operational efficiency.
While these similarities create a foundation for their effectiveness in manufacturing, it is in their differences that the distinct advantages of each type of robot become evident.
Cobot vs. robot: The differences
The differences between robots and cobots can be found on multiple levels, making them suitable for distinctive applications:
Physical interaction
- Cobots: Engineered for safe physical interaction with humans, cobots operate alongside workers without the need for physical barriers. They incorporate advanced safety features, such as force and proximity sensors, to ensure a secure working environment.
- Robots: Traditional industrial robots typically operate in fenced-off areas, physically separated from human workers. They lack the safety features necessary for close collaboration, focusing more on autonomous task execution.
Programming and flexibility
- Cobots: Cobots are designed for ease of programming, allowing non-experts to teach them new tasks. Their flexibility enables quick adaptability to different applications without extensive reprogramming, making them suitable for diverse tasks.
- Robots: Programming traditional robots can be more complex, often requiring specialized expertise. They are optimized for performing specific tasks efficiently, but may involve longer setup times when reconfiguring large units for different applications.
Application range
- Cobots: Cobots excel in scenarios where tasks require human collaboration, such as assembly or small-scale production. They are well-suited for industries that demand flexibility and frequent task changes.
- Robots: Traditional robots are effective in mass production setups, where tasks are repetitive and do not require human interaction. They are commonly employed in automotive, electronics, and heavy manufacturing industries, but also in certain pharmaceutical applications.
Process automation with ESSERT Robotics
ESSERT Robotics is at the forefront of revolutionizing industrial automation with two standout solutions: the ADVANCED Robotic Workstation and the ESSERT MicroFactory.
The ADVANCED Robotic Workstation, crafted for optimum functionality and user-friendly operation, serves as a flexible solution catering to a variety of applications. With robust protection technology and an array of robotic components, it is specifically tailored for high mix / low volume production, providing unmatched versatility and efficiency. It can be operated both as an autonomous workstation or in collaboration with human workers, making it an extremely versatile and agile system.
The ESSERT MicroFactory, built on the modular architecture of the ADVANCED Robotic Workstation, introduces unprecedented flexibility to high mix / low volume scenarios. Its modular design enables customized compositions, independent commissioning of process modules, and effortless scalability.
Read more about robotics
Robots in manufacturing: revolutionizing production processes
Robotic manufacturing companies
Cobot – all you need to know about collaborative robots
What is an industrial robot?
Robotics in the pharmaceutical industry
Robotics – 7 facts you need to know
- Industrial Robots. Definition. IFR. 2/2024. https://ifr.org/industrial-robots ↩︎
- Cobots: Robots for collaboration with people. 2/2024. https://peshkin.mech.northwestern.edu/cobot/ ↩︎